U-PVC Pipe Extrusion Line
Kitech provides a full range of pipe extrusion equipment and production process for u-PVC, m-PVC and c-PVC pipes for all types of water supply, drainage, sewage, threading, fire, drilling and other application. Kitech adopts SJZ series of conical and SJP series of parallel twin-screw extruders, single / double spider type die head, 2/3/4/6/8 multi-track haul-off, with chamfering function planetary saw cutter, U/ R and rectangular type belling machine. Our line can be used for processing the largest diameter up to 800mm, wall thickness range of 1-30mm.
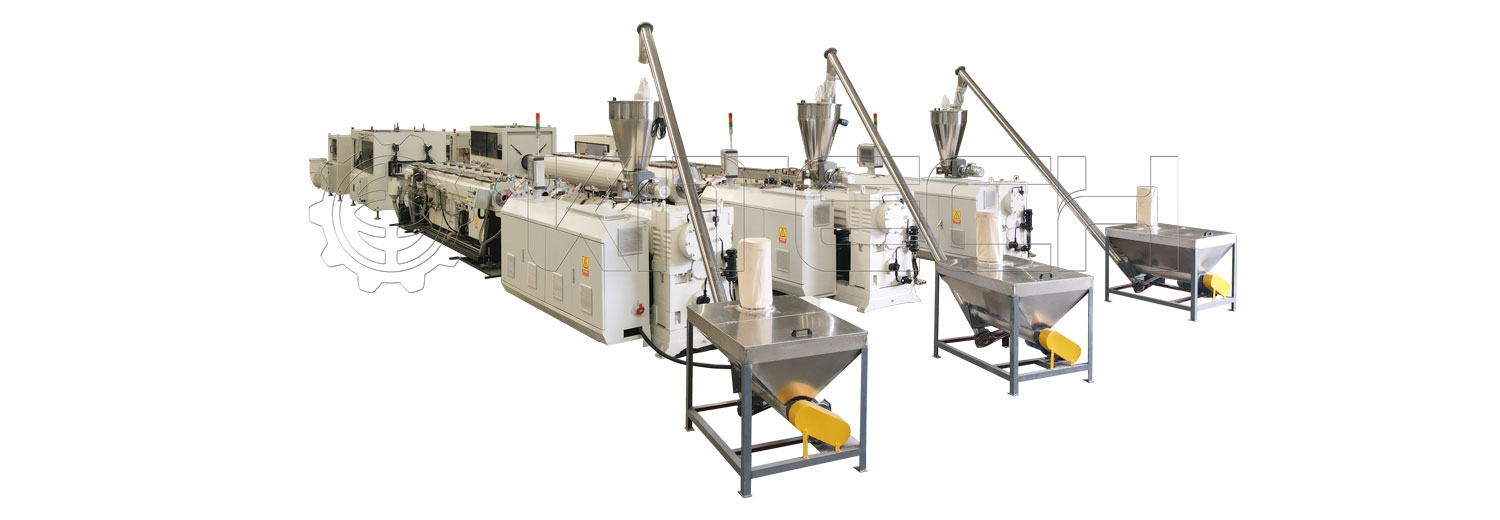
Product Category
Contact Us
- 86-13773222278
- 86-512-58962530
- [email protected]
- 7-1 Workshop Jiulong Logistic Park, Jinfeng Town, Zhangjiagang City, Jiangsu China
Special screw structure, effective melt plasticizing and for different type of formula;
Flexible use conical and parallel extruder for pipes with different pressure levels and CaCO3 conditions;
Spider type die reduces the melt seam on pipes, high compression ratio ensures the pipes with high density and good mechanical properties.
Use an efficient single or double chambers and station 4-12m long vacuum and cooling unit;
Adopt a Servo/frequency speed controlling and independent multi-track structure haul-off to guarantee the pipe pulling evenly, no deformation;
Planetary cutter adopts both mechanical and hydraulic way to feed blades and to cut and chamfer synchronously.
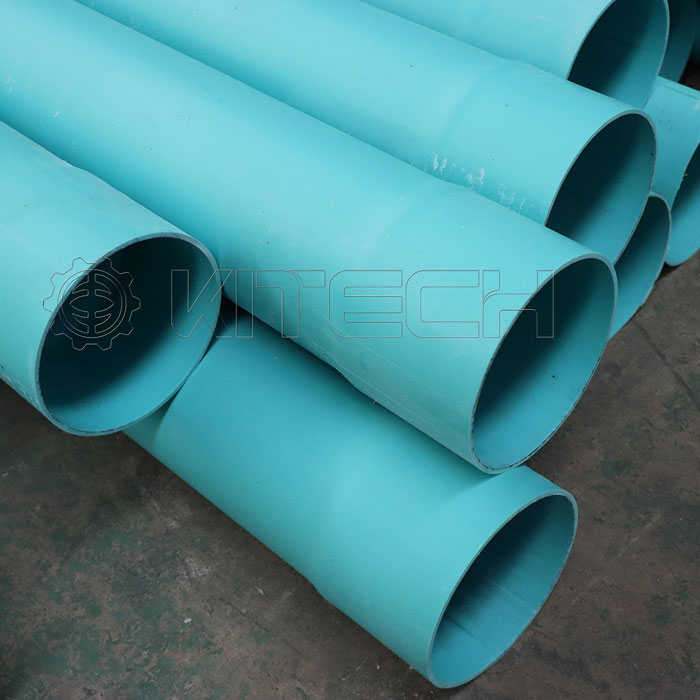
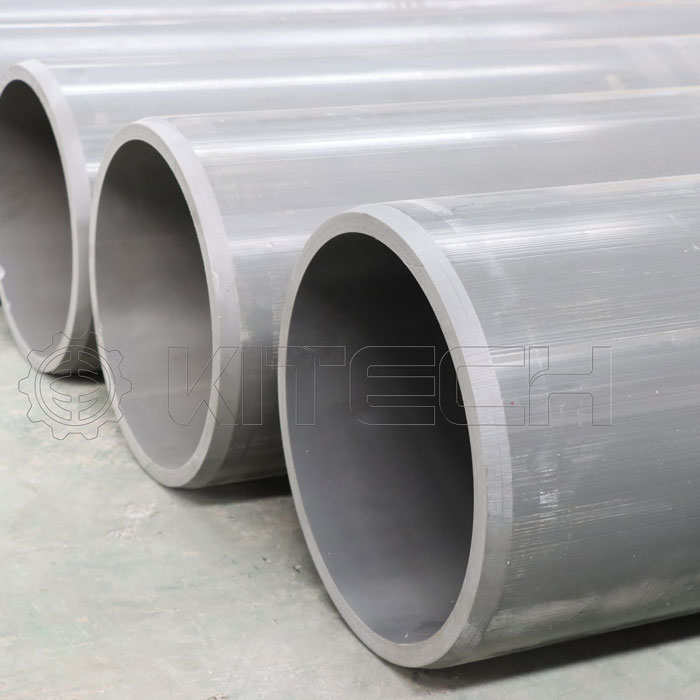
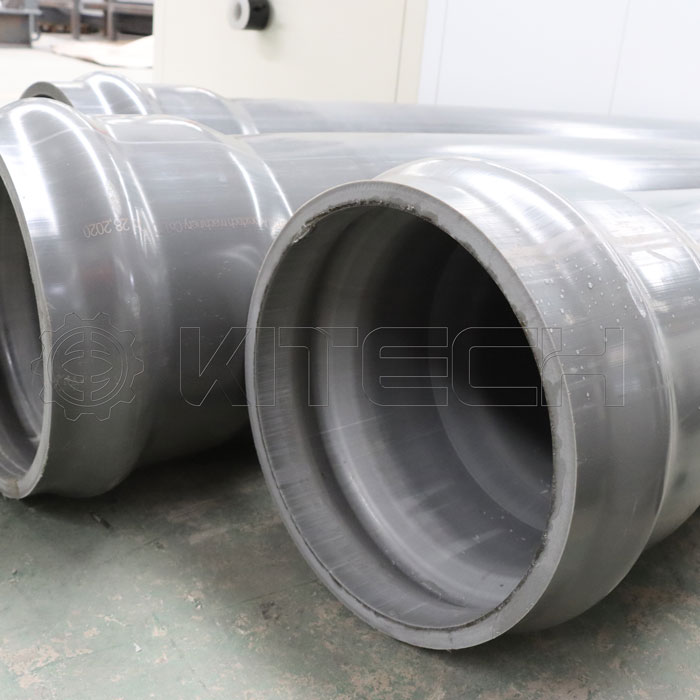
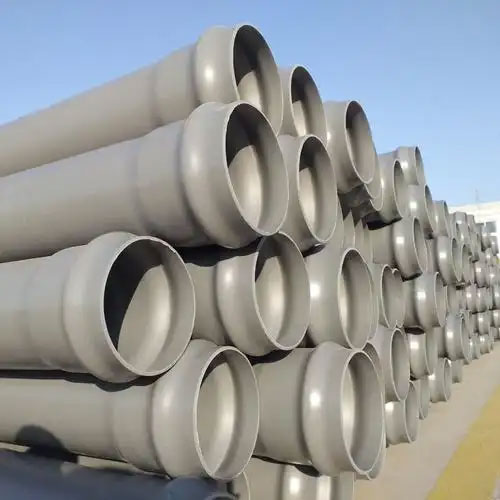
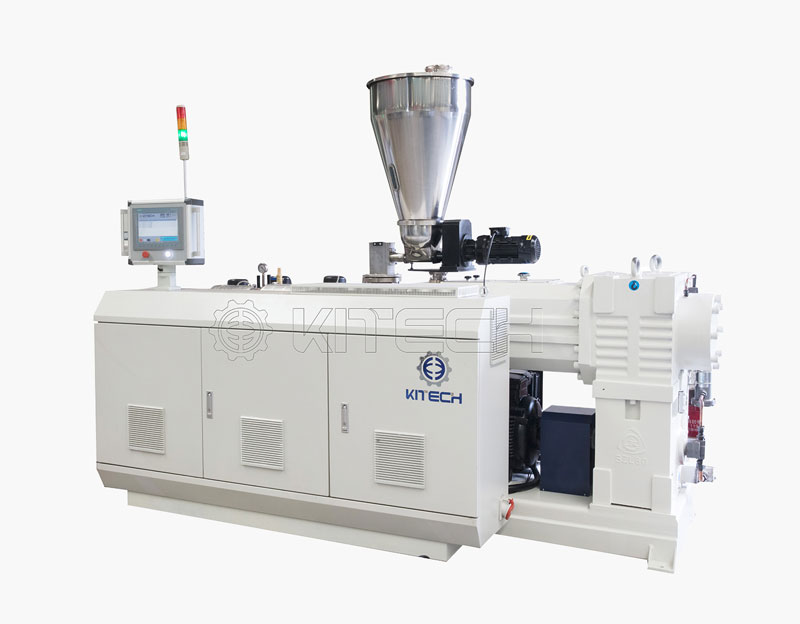
Conical twin screw extruder
– Siemens/WEG original motor achieved global after service;
– Bimetallic screw and barrel;
– Intelligent PLC controlling system with human-friendly interface.
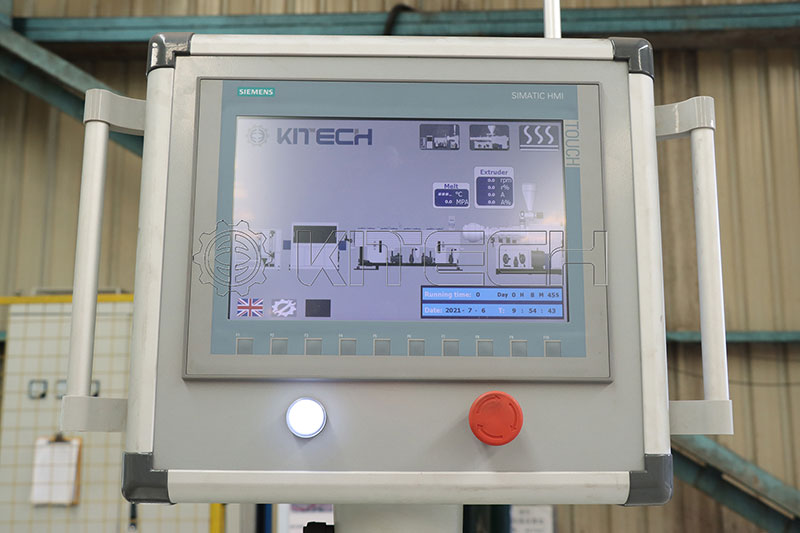
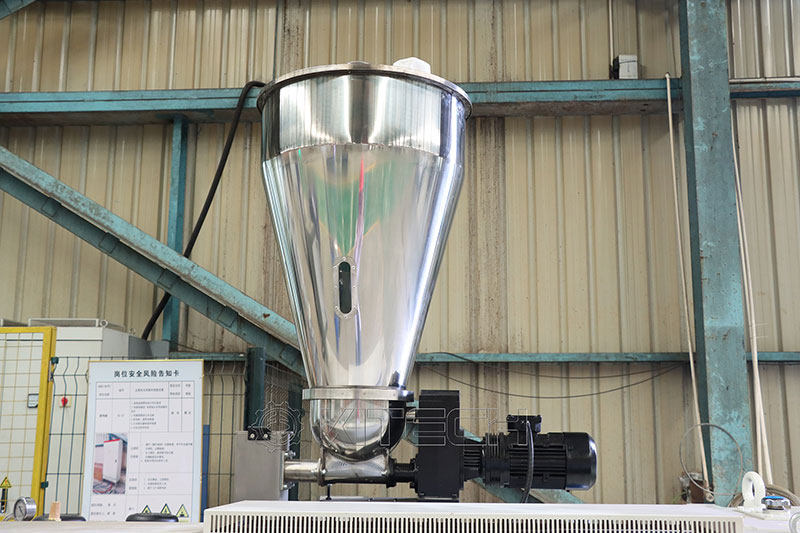
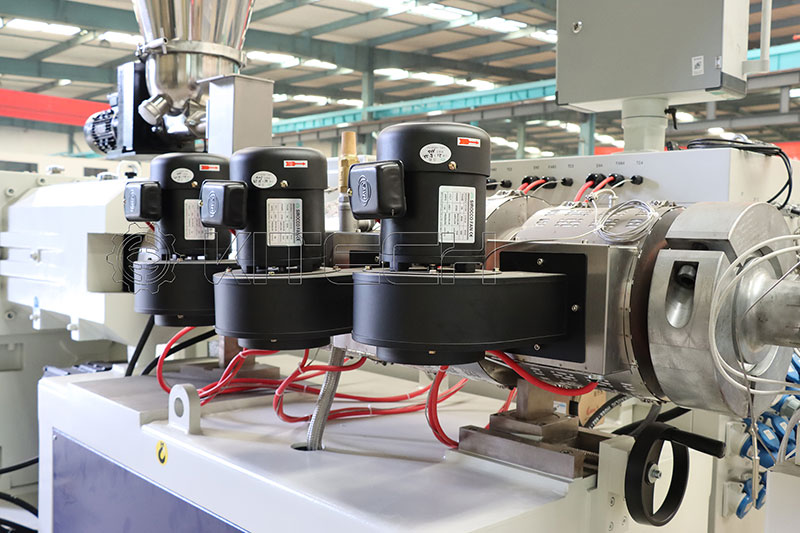
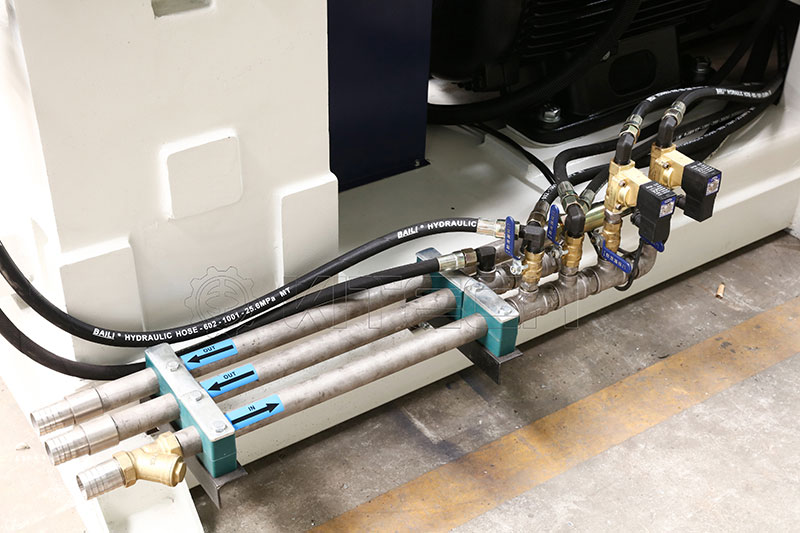
Mould
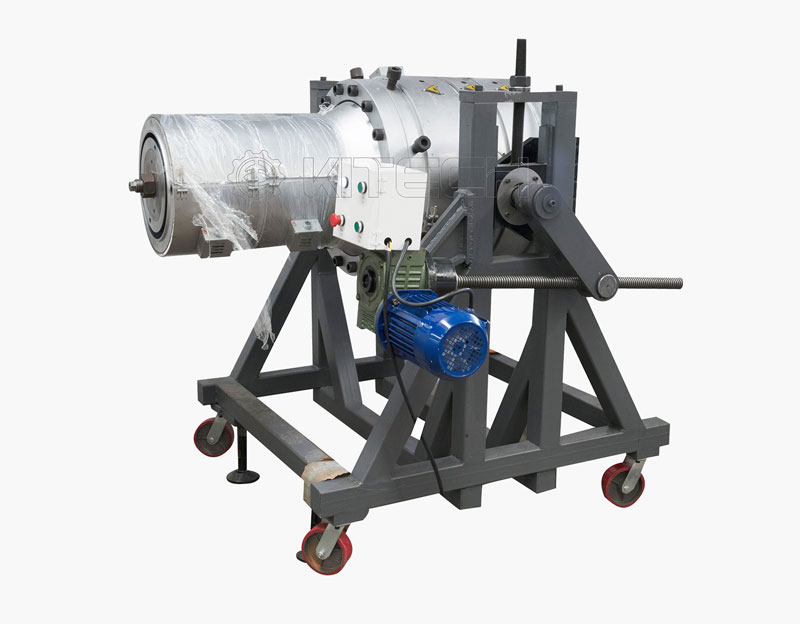
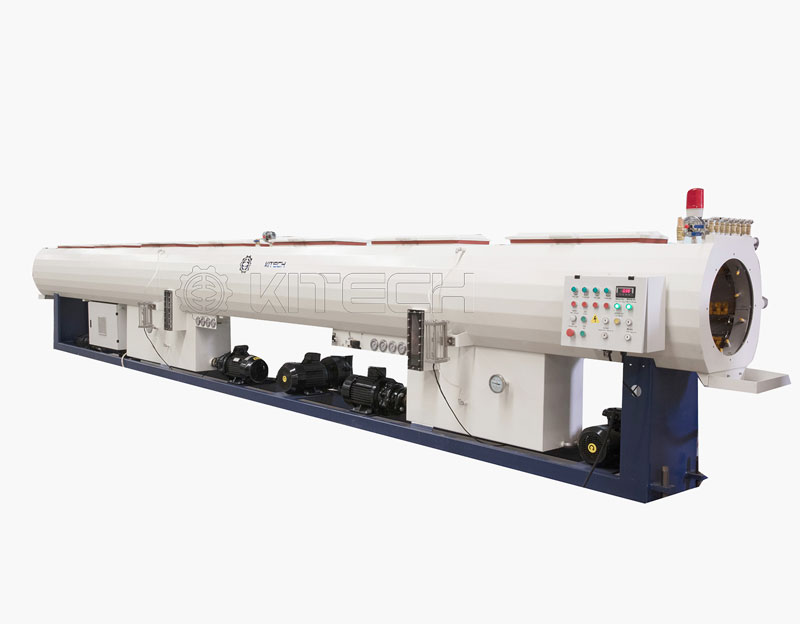
Water Cooling Tank
It’s primarily used to control the temperature of various equipment and molds to ensure smooth production and prevent overheating, especially when processing materials like PVC.
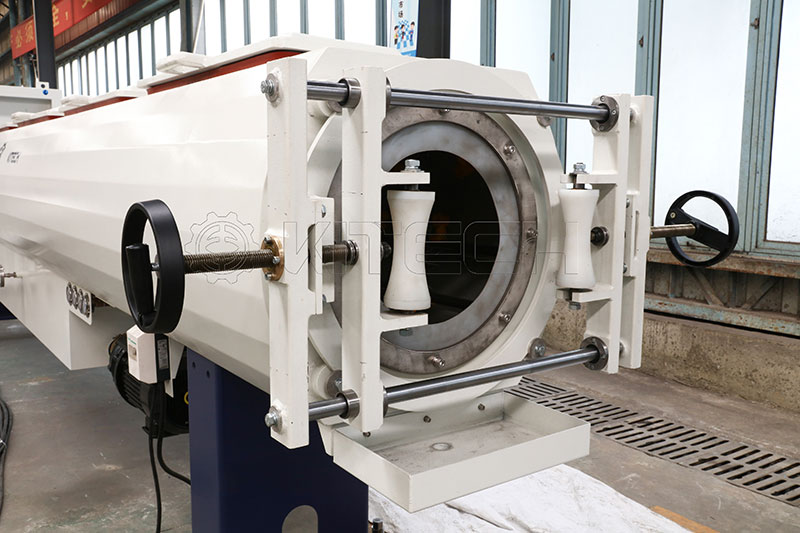
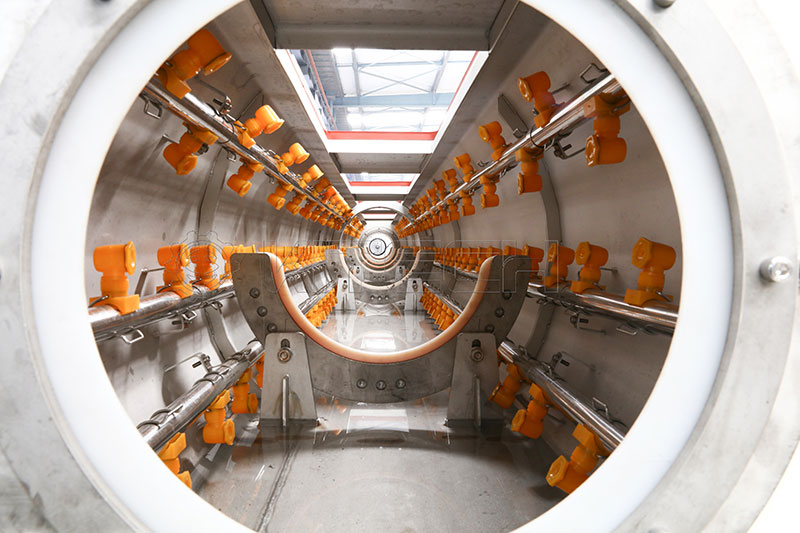
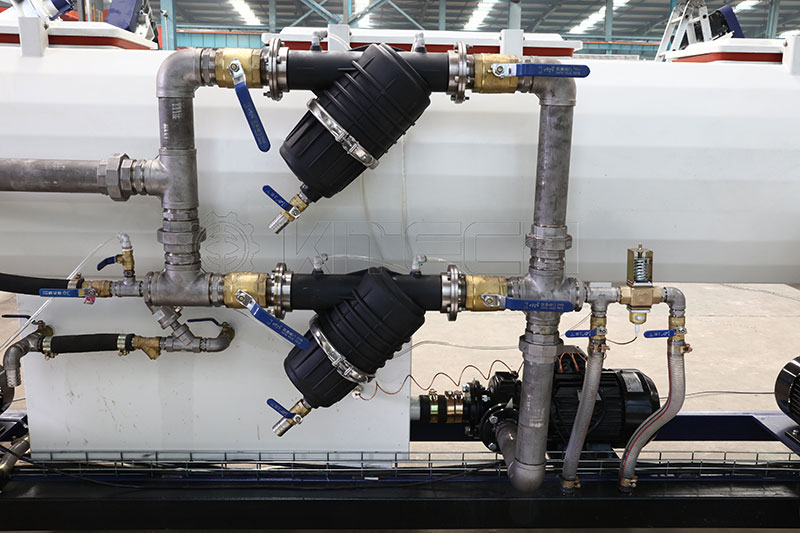

Haul off Machine
– Fast change type pads
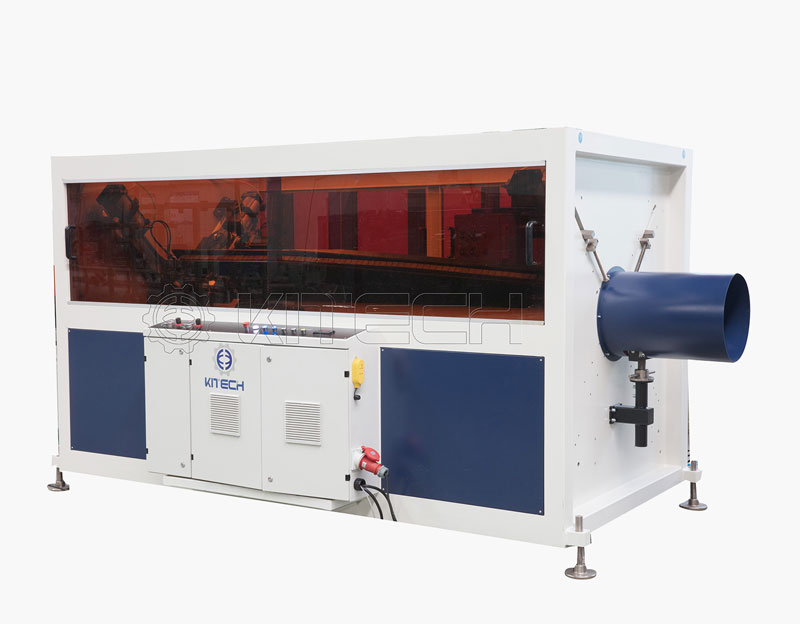
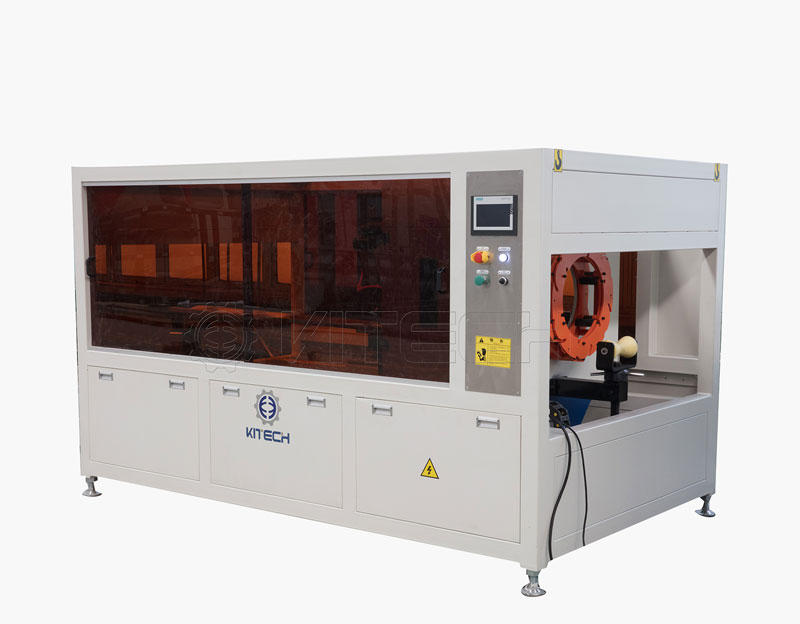
Cutting Machine
The cutting machine, typically synchronized with the extrusion speed, is used to precisely cut the extruded pipes or profiles into individual sections of the desired length.

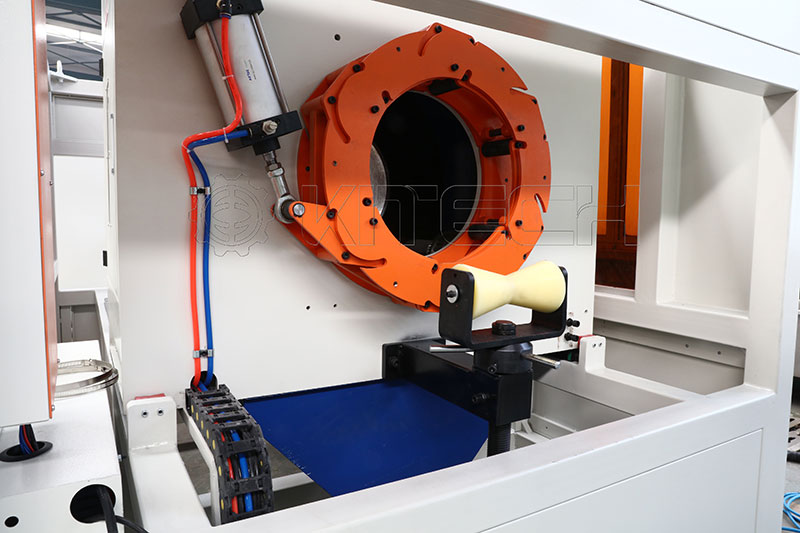
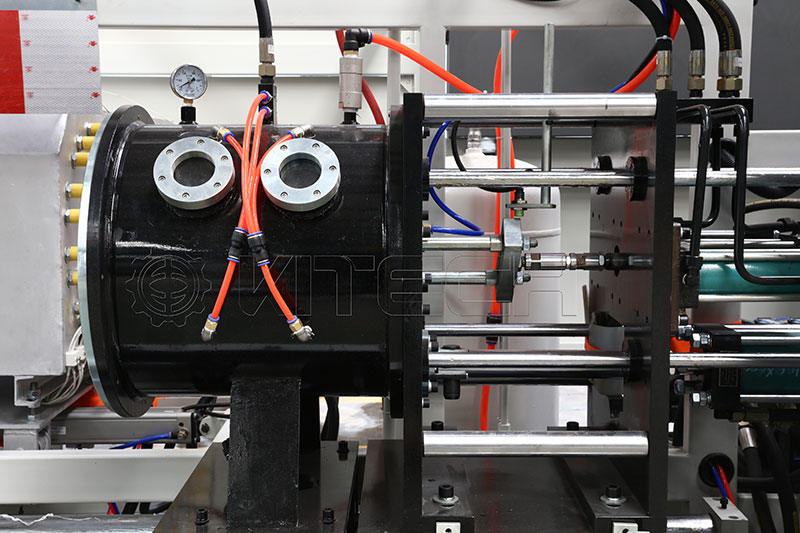
Belling Machine
– Socket forming: shaped for insertion of rubber gasket (blowing system)
– Socket forming: collapsible system
– Socket forming: auto-load rubber gasket
– Touch screen control panel
– User friendly software developed
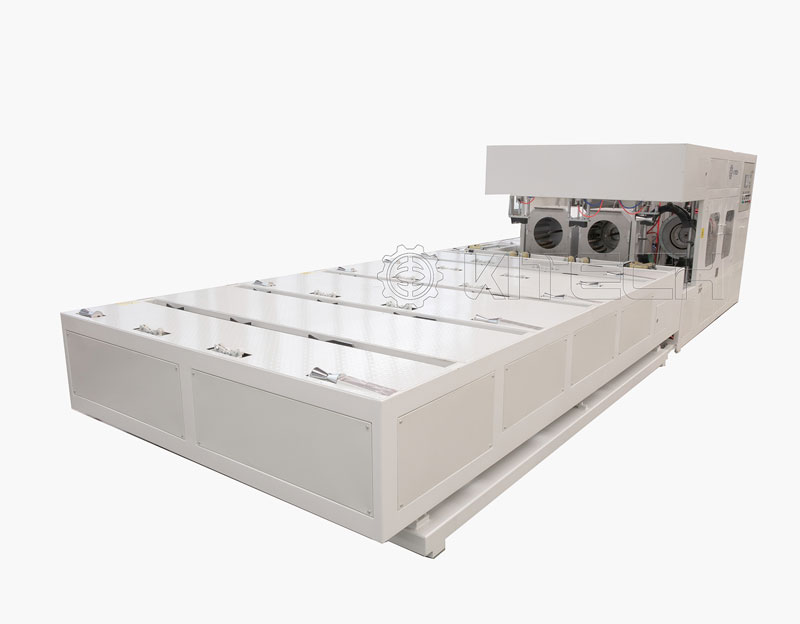
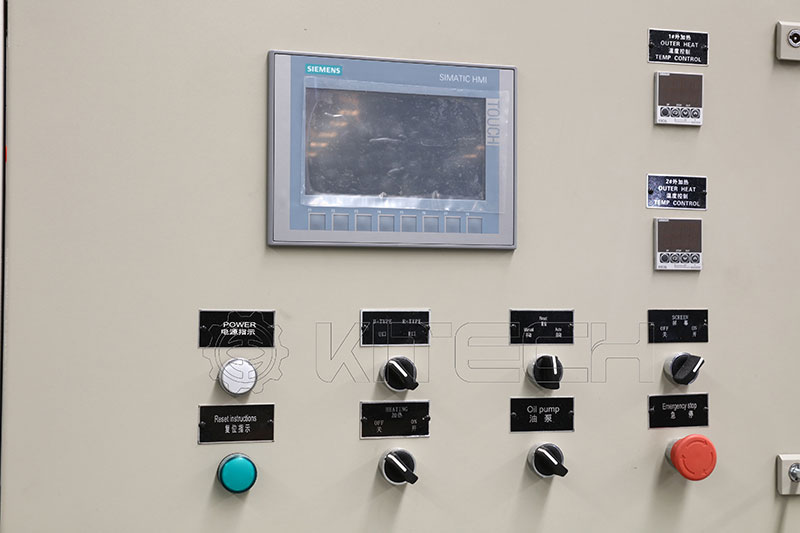
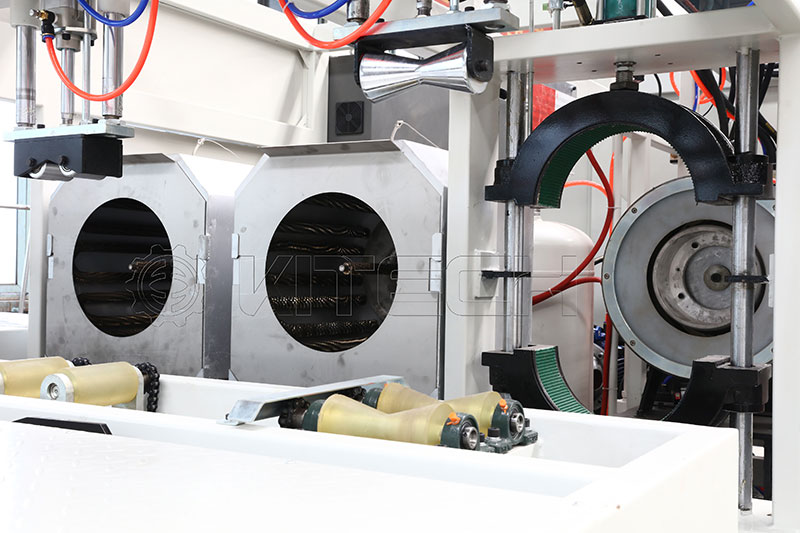
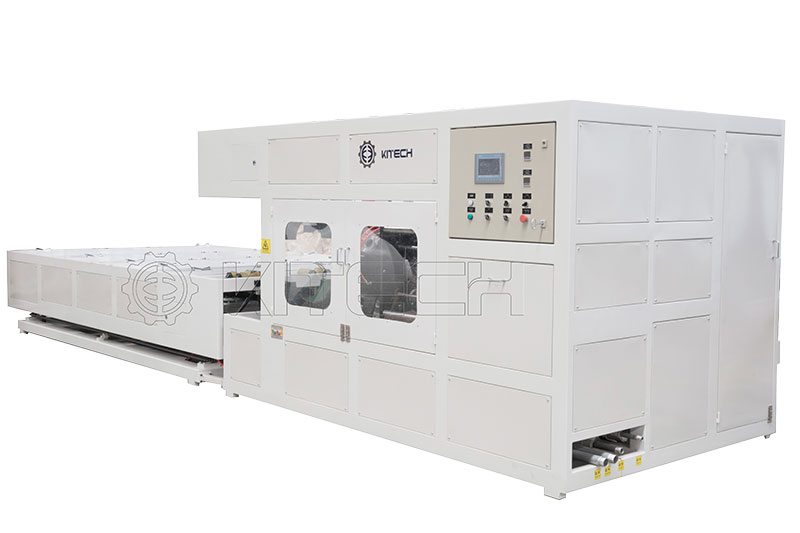
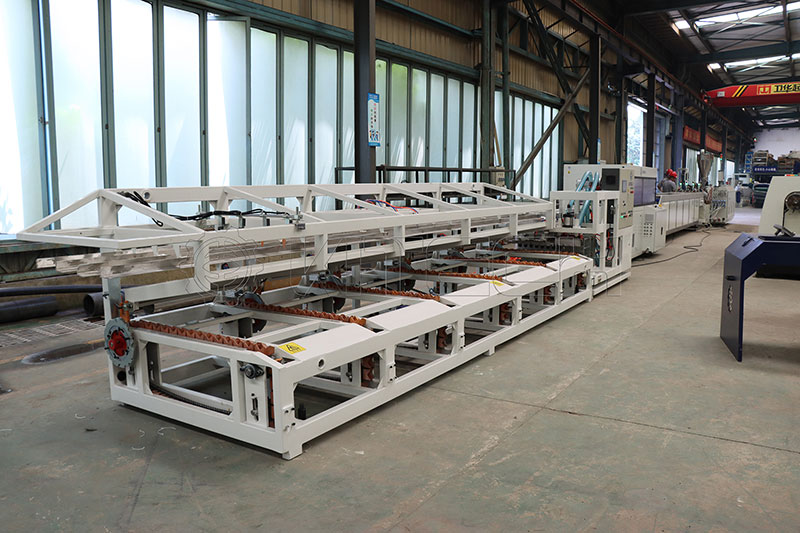
Stacker
Air cylinder turn over
Stack and discharge separately
Model | O.D. (mm) | Extruder | Max. output(kg/h) | Max. Haul-off speed (m/min) | Motor Power(kW) |
---|---|---|---|---|---|
PVC32 Four | Ф16-32 | SJZ65/132 | 250 | 8*4 | 37AC |
PVC40 Dual | Ф16-40 | SJ51/105 | 120 | 8*2 | 18.5AC |
PVC63 Dual | Ф20-63 | SJZ65/132 | 250 | 12*2 | 37AC |
PVC63 Single | Ф20-63 | SJZ55/110 | 180 | 12 | 22AC |
PVC110 Single | Ф40-110 | SJZ65/132 | 250 | 6 | 37AC |
PVC110 Dual | Ф40-110 | SJZ80/156 | 400 | 6*2 | 55AC |
PVC160 | Ф50-160 | SJZ65/132 | 250 | 5 | 37AC |
PVC200 | Ф63-200 | SJZ80/156 | 350 | 6 | 55AC |
PVC250 | Ф75-250 | SJZ80/156 | 400 | 5.5 | 55AC |
PVC315 | Ф110-315 | SJZ80/156 | 400 | 5 | 75AC |
PVC400 | Ф160-450 | SJZ92/188 | 600 | 3.5 | 110AC |
PVC630 | Ф315-630 | SJZ92/188 | 800 | 2 | 110AC |
PVC800 | Ф500-800 | SJP130/28 | 1100 | 1.3 | 160AC |